В книге изложены современные представления о процессах выплавки, внепечной обработки и непрерывной разливки стали. Приведены особенности конструкций и работы различных технологических комплексов, а также современной техники и технологии на различных этапах производства стали. Особое внимание уделено технологии получения стали на агрегате ковш-печь. Рассмотрены конструктивные особенности агрегатов, основные принципы конструирования и технологические параметры во взаимосвязи с энергетическими режимами при оптимизации условий перемешивания металла в процессе работы. Обоснованы новые направления технологии использования порошковых проволок для производства стали Показаны особенности технологии производства различных групп марок стали в современных условиях - с нормированным содержанием серы, борсодержащих, коррозионностойких, кордовых, железнодорожного сортамента и др. Значительное внимание уделено использованию редкоземельных металлов в сталеплавильном производстве, технологическим и конструктивным параметрам МНЛЗ и качеству непрерывнолитой стальной заготовки.
В книге обобщен отечественный и зарубежный опыт на достигнутом уровне развития сталеплавильного производства, а также представлены материалы по теоретическим и практическим разработкам авторов, которые проверены и используются на ряде металлургических предприятий.
Книга предназначена для научных и инженерно-технических работников металлургических и машиностроительных предприятий и научно-исследовательских институтов. Может быть полезна преподавателям, аспирантам и студентам вузов металлургического профиля.
Рекомендована к печати ученым советом Донецкого национального технического университета.
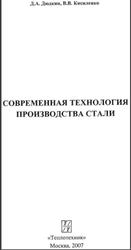
Повышение производительности конвертеров.
Вопрос повышения производительности конвертеров представляется наиболее актуальным в ракурсе увеличения объемов производства стали в действующих цехах, большинство из которых было построено два и более десятилетий назад. Для повышения эффективности конвертерной плавки на современных производствах все большее распространение получают методы контроля положения и конструкции верхней фурмы, скорости вдувания кислорода, повышения эффективности процесса шлакообразования, оптимизации параметров вдувания аргона через донные фурмы, а также оперативного прогнозирования содержания углерода по ходу продувки. При этом увеличение производительности конвертеров рассматривается в большинстве случаев как системное мероприятие, предполагающее увеличение доли используемого металлолома, расширение внедоменной обработки чугуна, радикальное повышение стойкости футеровки, интенсификации процесса плавки за счет комбинированной продувки, обеспечение надежной системы отсечки шлака при выпуске из конвертера, повышение эффективности обработки стали в ковше. Так, в конвертерном цехе металлургического завода "Voestalpine Stahl" (Линц, Австрия), имеющем в своем составе три 160-тонных конвертера, достигнута годовая производительность 4,8 миллиона тонн стали, что соответствует 30700 плавкам в год (87 плавок в день) [5]. При этом расход металлолома возрос до 355 кг/т стали (расход жидкого чугуна уменьшился при этом до 782 кг/т). Конструкция конвертера (рабочий объем 104 м3) предполагает комбинированную продувку с установкой в днище 12 продувочных узлов для инжектирования аргона. Отсечка шлака на выпуске осуществляется газодинамическим устройством. Доводка стали в ковше выполняется на двух агрегатах ковш-печь и двух вакууматорах RH.
На металлургическом заводе "Port Talbot Works" (Великобритания) удалось повысить производительность конвертерного цеха (2 конвертера с массой плавки 326 тонн каждый, 2 вакууматора RH-OB, 2 агрегата для обработки стали в ковше типа CAS-OB/DeS и 3 МНЛЗ) с 3,8 миллиона тонн до 4,8 миллиона тонн жидкой стали в год. Это соответствует в среднем 43 плавкам в сутки при рабочем цикле выпуска плавок из конвертера менее 35 минут. Для обеспечения такого цикла работы практически весь жидкий чугун подвергается десульфурации перед заливкой в конвертер, причем значительная часть чугуна (при выплавке качественных сталей) - глубокой десульфурации. Время выпуска стали из конвертера было уменьшено с 7 до 5,5 минуты за счет увеличения диаметра сливного отверстия, масса плавки возросла до 240 тонн, а период продувки металла был уменьшен на 1,5 минуты за счет увеличения расхода кислорода с 950 до 1000 м в минуту.
ОГЛАВЛЕНИЕ.
ВВЕДЕНИЕ.
Глава 1. СОВРЕМЕННЫЕ ТЕНДЕНЦИИ ПРОИЗВОДСТВА СТАЛИ.
1.1. Особенности современного этапа сталеплавильного производства в мире.
1.2. Состояние и перспективы кислородно-конвертерного процесса.
1.2.1. Развитие кислородно-конвертерного производства стали.
1.2.2. Разновидности кислородно-конвертерного процесса производства стали.
1.2.3. Повышение производительности конвертеров.
1.2.4. Особенности внепечной обработки металла в конвертерных цехах.
1.3. Развитие металлургических мини-заводов.
1.4. Современное состояние и перспективы развития электродуговых сталеплавильных печей.
1.4.1. Дуговые печи переменного и постоянного тока.
1.4.2. Варианты конструктивного исполнения дуговых электропечей.
1.4.3. Перспективы электросталеплавильного производства в XXI веке.
Глава 2. ОРГАНИЗАЦИЯ ВЫПУСКА МЕТАЛЛА ИЗ ПЛАВИЛЬНОГО АГРЕГАТА В СТАЛЕРАЗЛИВОЧНЫЙ КОВШ.
2.1. Температура металла на выпуске.
2.2. Организация выпуска металла в сталеразливочный ковш.
2.3. Отсечка шлака при сливе металла из сталеплавильного агрегата.
Глава 3. ПОЛУЧЕНИЕ СТАЛИ НА АГРЕГАТЕ КОВШ-ПЕЧЬ.
3.1. Ковш-печь - современный агрегат для получения стали заданного качества.
3.1.1. Назначение агрегата ковш-печь.
3.1.2. Сопоставление технологии внепечной обработки на установках комплексной доводки стали и агрегатах ковш-печь.
3.1.3. Классификация агрегатов ковш-печь в зависимости от условий производства.
3.1.4. Технологический комплекс внепечной обработки стали: агрегат ковш-печь - вакууматор.
3.2. Технологическое оборудование агрегата ковш-печь.
3.2.1. Конструктивные особенности агрегата ковш-печь.
3.2.2. Агрегаты ковш-печь на постоянном токе.
3.2.3. Агрегаты ковш-печь с плазменным нагревом металла.
3.3. Рафинировочный шлак агрегата ковш-печь.
3.3.1. Требования, предъявляемые к рафинировочному шлаку.
3.3.2. Особенности формирования рафинировочных шлаков.
3.3.3. Химический состав рафинировочного шлака для сталей, раскисленных алюминием.
3.3.4. Химический состав рафинировочного шлака для сталей, раскисленных кремнием.
3.3.5. Требования к шлакообразующим материалам.
3.3.6. Скорость формирования рафинировочного шлака и его десульфурирующая способность.
3.3.7. Оптимальное количество шлакообразующих, присаживаемых в ковш и оптимальная толщина шлакового слоя.
3.4. Продувка металла инертным газом.
3.4.1. Влияние перемешивания металла со шлаком на процесс десульфурации.
3.4.2. Удаление неметаллических включений.
3.4.3. Изменение содержания газов в стали.
3.4.4. Усреднение химического состава и температуры стали.
3.4.5. Сопоставление продувки металла в ковше сверху и снизу.
3.4.6. Оптимальное расположение и обслуживание продувочных пробок, интенсивность продувки.
3.5. Огнеупоры агрегата ковш-печь.
3.6. Электрические характеристики агрегата ковш-печь.
3.7. Тепловой и материальный баланс агрегата ковш-печь.
3.7.1. Методика определения теплового баланса.
3.7.2. Структура теплового баланса.
3.7.3. Пути снижения расхода электрической энергии.
3.7.4. Сопоставление затрат электроэнергии на агрегатах "ковш-печь" различных предприятий.
3.8. Технологический режим агрегата ковш-печь.
3.8.1. Технология обработки стали шлаком.
3.8.2. Расчет количества шлакообразующих, присаживаемых на ковше-печи.
3.8.3. Режим продувки металла аргоном.
3.8.4. Оптимальный расход ферросплавов.
3.8.5. Электрический режим обработки.
3.8.6. Десульфурация стали.
3.8.7. Окисленность металла.
Глава 4. ОБРАБОТКА СТАЛИ ПОРОШКОВЫМИ ПРОВОЛОКАМИ.
4.1. Конструктивные решения и расположение оборудования для ввода проволок.
4.2. Обработка стали кальцийсодержащими реагентами.
4.2.1. Технологические аспекты внепечного рафинирования стали с применением кальция.
4.2.2. Комплексное воздействие кальция на свойства жидкой и твердой стали.
4.2.3. Внепечная обработка стаж порошковой проволокой с наполнением силикокальцием СК40.
4.3. Технология производства стали с регламентированным содержанием элементов в узких пределах.
4.3.1. Науглероживание стали.
4.3.2. Микролегирование стали титаном.
4.3.3. Микролегирование стали ванадием.
Глава 5. ПРОИЗВОДСТВО СПЕЦИАЛЬНЫХ МАРОК СТАЛИ В СОВРЕМЕННЫХ УСЛОВИЯХ.
5.1. Технология производства стали с нормированным содержанием серы.
5.1.1. Разработка технологии внепечной обработки стали серосодержащей порошковой проволокой.
5.1.2. Технология внепечной обработки стали порошковыми проволоками с двойным вводом кальция.
5.1.3. Практические правила обработки сталей с нормированным содержанием серы порошковыми проволоками.
5.2. Производство борсодержащих марок стали.
5.2.1. Влияние бора на качество и свойства различных марок стали.
5.2.2. Разработка технологии внепечной обработки различных групп марок стали борсодержащей порошковой проволокой.
5.2.3. Анализ качества и служебных свойств стали, микролегированной бором.
5.2.4. Рекомендации по оптимальной технологии внепечной обработки стали борсодержащей проволокой.
5.3. Производство колесной стали с модифицированием силикокальцием.
5.3.1. Анализ современного состояния производства колесной стали.
5.3.2. Технология выплавки, внепечной обработки и разливки колесной стали.
5.3.3. Модифицирование колесной стали.
5.3.4. Внепечная обработка колесной стали силикокальцием и титаном в составе порошковой проволоки.
5.4. Особенности технологии производства рельсовой стали с микролегированием комплексным сплавом КМКТ.
5.5. Производство стали кордового сортамента, модифицированной кальцием.
5.6. Технология производства коррозионностойких трубных марок стали.
5.6.1. Коррозионно-активные неметаллические включения.
5.6.2. Некоторые пути снижения общей загрязненности трубной стали неметаллическими включениями.
5.6.3. Практические рекомендации по технологии производства коррозионностойких марок стали.
5.7. Технология производства литейной стали с ковшевым раскислением алюмокальциевой проволокой.
5.7.1. Анализ существующей технологии производства литейной стали.
5.7.2. Оптимизация технологии раскисления стали 20ГЛ.
5.7.3. Исследование технологии производства литейной стали с новым режимом раскисления.
5.7.4. Технологические особенности раскисления стали порошковой проволокой.
5.7.5. Влияние внепечной обработки алюмокальциевой порошковой проволокой на охлаждение металла в ковше.
5.7.6. Качество и механические характеристики стали 20ГЛ.
Глава 6. РЕДКОЗЕМЕЛЬНЫЕ МЕТАЛЛЫ В СТАЛЕПЛАВИЛЬНОМ ПРОИЗВОДСТВЕ.
6.1. Использование редкоземельных металлов для микролегирования и модифицирования жидкой стали.
6.2. Поведение редкоземельных металлов в металлургических расплавах.
6.2.1. Взаимодействие редкоземельных металлов с основными элементами, содержащимися в стали.
6.2.2. Термодинамические условия образования редкоземельных включений в жидком металле.
6.2.3. Формирование редкоземельных оксидов.
6.2.4. Формирование редкоземельных сульфидов.
6.2.5. Условия формирование редкоземельных оксисульФидов.
6.2.6. Взаимодействие РЗМ с окислами металлов.
6.3. Разработка эффективных составов комплексных модификаторов, содержащих кальций и редкоземельные металлы.
6.4. Промышленные исследования комплексной технологии раскисления и внепечной обработки трубной стали.
6.4.1. Технология раскисления и внепечной обработки комплексным модификатором с РЗМ трубной стали марки 20СА.
6.4.2. Условия проведения опытно-промышленных плавок коррозионностойких трубных марок стали (13ХФА, 20СА, 20КТ).
6.4.3. Внепечная обработка трубной стали на агрегате ковш-печь проволокой с наполнением комплексным модификатором Са+РЗМ.
6.4.4. Анализ усвоения церия и лантана из комплексного модификатора.
6.4.5. Анализ неметаллических включений в металле.
6.4.6. Загрязненность трубной стали неметаллическими включениями.
6.4.7. Микроструктура металла труб после термической обработки.
6.4.8. Коррозионные характеристики металла труб после термической обработки.
6.4.9. Выход годного металла на опытных и сравнительных плавках.
6.5. Рекомендации по оптимальной комплексной технологии раскисления и внепечной обработки коррозионностойкой трубной стали.
Глава 7. ТЕХНОЛОГИЧЕСКИЕ И КОНСТРУКТИВНЫЕ АСПЕКТЫ СОВРЕМЕННЫХ МНЛЗ.
7.1. Современное состояние процессов непрерывного литья стали.
7.2. Промежуточное разливочное устройство.
7.3. Кристаллизаторы МНЛЗ.
Глава 8. КАЧЕСТВО НЕПРЕРЫВНОЛИТОЙ СТАЛЬНОЙ ЗАГОТОВКИ.
8.1. Особенности кристаллизации и неоднородность непрерывнолитого слитка.
8.2. Функциональные особенности шлакообразующих смесей для кристаллизаторов.
8.3. Непрерывное литье стали с использованием электромагнитных систем.
8.4. Пути снижения осевой ликвации и пористости.
Глава 9. ВНЕПЕЧНАЯ ОБРАБОТКА ПЕРЕДЕЛЬНОГО ЧУГУНА В СОВРЕМЕННЫХ УСЛОВИЯХ.
9.1. Анализ задач и способов внепечной обработки чугуна.
9.2. Внедоменная десульфурация передельного чугуна.
9.3. Комплексное внепечное рафинирование чугуна.
СПИСОК ЛИТЕРАТУРЫ.
Бесплатно скачать электронную книгу в удобном формате, смотреть и читать:
Скачать книгу Современная технология производства стали, Дюдкин Д.А., Кисиленко В.В., 2007 - fileskachat.com, быстрое и бесплатное скачивание.
Скачать djvu
Ниже можно купить эту книгу, если она есть в продаже, и похожие книги по лучшей цене со скидкой с доставкой по всей России.Купить книги
Скачать - djvu - Яндекс.Диск.
Дата публикации:
Теги: учебник по машиностроению :: машиностроение :: Дюдкин :: Кисиленко :: металлургия
Смотрите также учебники, книги и учебные материалы:
Следующие учебники и книги:
Предыдущие статьи: